OVERVIEW
Introducing M36O
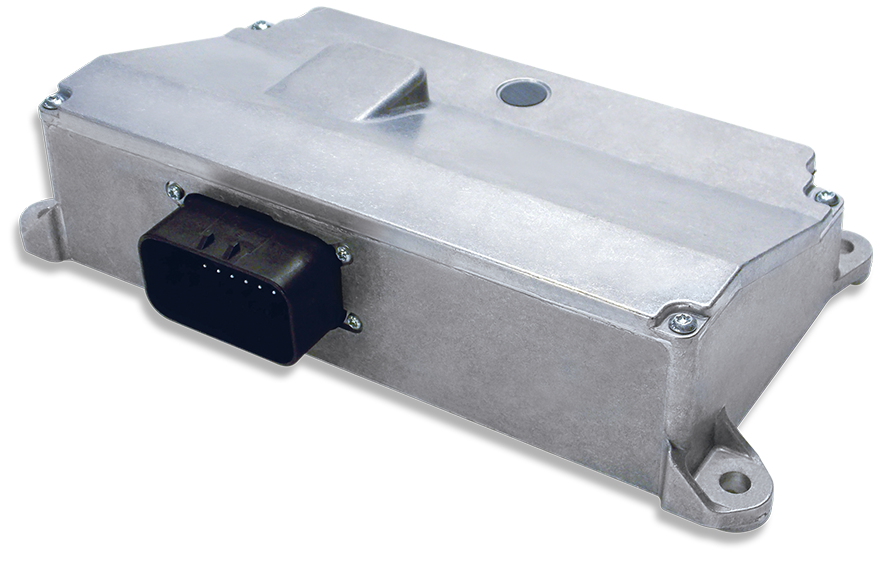
OpenECU™ M360
M360 OpenECU is designed to support high current applications with a favorable functional safety ISO 26262 architecture. M360 is designed with two H-bridges capable of 50 A of transient current. These H-bridges can be used to control brushed-DC Motor automotive applications. Applications include Electric Park Brake (EPB) or Electric Parking Brake (EPB) ECU development.
M360 has a dual-microcontroller architecture with asymmetric hardware and software redundancy.
The high-performance MPC5746B microprocessor supported by the powerful 32-bit SPC560P34 secondary microprocessor provides for sophisticated, high-bandwidth rationality checking and system safety monitoring of full-authority vehicle control applications.
Features
- Powerful dual micro-processor architecture with intermicro serial comms for program flow monitoring and 1x shared external CAN channel from both micros
- 2x H-bridges for high current outputs (10A continuous, 50A transient for 100ms)
- Comprehensive fault diagnosis supporting functional safety as well as OBD requirements
- High level diagnostics fault reporting resident in platform software
- Platform SW supports light-duty J1979/KWP2000/UDS 14229 and Heavy-duty J1939 service tool interfaces
- Supported platform software: OpenECU-FS
High Performance
- Powerful dual micro-processor architecture with inter-micro serial comms for program flow monitoring and 1x shared external CAN channel from both micros
- 2x H-bridges for high current outputs (10A continuous, 50A transient for 100ms)
- Comprehensive fault diagnosis supporting functional safety as well as OBD requirements
- High level diagnostics fault reporting resident in platform software
- Platform SW supports light-duty J1979/KWP2000/UDS 14229 and Heavy-duty J1939 service tool interfaces
Capabilities
- Designed for high current brushed-DC motor control applications
- Adopted in functional safety and high transient current applications such as Electronic Park Brake
- Supports common calibration tools such as ATI Vision and Vector CANape via CCP
- Proven hardware for prototyping, pre-production and volume production
Hardware Specifications
Primary Processor | MPC5746B |
Secondary Processor | 32-bit |
Input Pins | 4 Analog inputs |
Output Pins | 4 (2x H-Bridges) |
H-Bridge Output | Continuous: 2x (10A), Transient: 2x (50A) for 100 ms |
Current Monitors | 2x current monitors per H-bridge for circuit, rationality and unintended actuation diagnostics – read by both micros |
Voltage Monitors | 2x voltage monitors (one on each arm) per H-Bridge for circuit and rationality diagnostics – read by both micros |
External Communication | 1x CAN (both micros have independent interface to the CAN bus) |
Internal Communication | 1x UART serial interface between the micros |
Dimensions | 207mm x 104mm x 45mm (W x D x H) |
EMC | Designed for DIN/ISO 11452, ISO 7637-2 and CISPR 25 |
Enclosure | Aluminum |
Weight | 0.54kg |
Connectors | 1×23 TE (AMPSEAL) |
Vibration | IEC 60068-2-64 |
Environmental Protection | IP69K & IPx8 Sealed/Gore vent |
APPLICATIONS
M360 Applications Include:
Application | Description |
Electric Parking Brake | M360 can be used as Electric Parking Brake (EPB) ECU replacing traditional mechanical parking brakes. The M360 as an EPB can control actuators to provide parking brake function and also dynamic braking as a secondary braking system. |
High Current H-Bridge Module | With 10A continuous and 50A peak (or transient) current H-Bridges M360 can be used in applications to control motors |
BLOCK DIAGRAM
This is a default configuration, optional configuration available, please contact us.
For a full list of downloads click here.
CASE STUDIES
DOWNLOADS
To view the complete list of our product downloads, please click here.
MODULE COMPARISON
Compare ALL OpenECU Modules
M110 | M130 | M211 | M220 | M6 Family | M670 | Actuation | M560 | M580 | |||||||||||
Microprocessor | |||||||||||||||||||
Primary Processor | SPC5534 | SPC5746B | MPC5534 | MPC5534 | MPC5534 | MPC5674F | MPC5746B | SPC5746 | SPC5746 | ||||||||||
Primary Clock Rate | 80MHz | 80MHz | 80MHz | 80MHz | 80MHz | 264MHz | 160MHz | 160MHz | 160MHz | ||||||||||
Primary Code Space | 512KB | 3MB | 768KB | 768KB | 512KB | 3MB | 2302KB | 3MB | 3MB | ||||||||||
Primary RAM Space | 64KB | 256kB | 832KB | 832KB | 64KB | 128kB | 384KB | 256KB | 256KB | ||||||||||
Primary Calibration Space | 256KB | 256kB | 236KB | 256KB | 256KB | 128kB | 128KB | 256KB | 256KB | ||||||||||
Secondary Processor | SPC560P34 | SPC560P34 | SPC560P34 | ||||||||||||||||
Secondary Clock Rate | 64MHz | 64MHz | 64MHz | ||||||||||||||||
Secondary Flash Space | 192KB | 192KB | 192KB | ||||||||||||||||
Secondary Calibration Space | 20KB | ||||||||||||||||||
Secondary RAM Space | 12KB | 12KB | |||||||||||||||||
M110 | M130 | M211 | M220 | M6 Family | M670 | Actuation | M560 | M580 | |||||||||||
Power | |||||||||||||||||||
Operating Voltage | 9V to 32V | 8V to 32V | 7V to 32 V | 7V to 32 V | 12V or 24V | 8V to 18V | 8V to 18V | 8V to 18V | |||||||||||
Sensor Supply | 1x 5V @250mA | 1x | 1 x 5V / 250mA | 1 x 5V / 250mA | 2x 5V@250mA | 4x 250mA @ 5V | none | 2x 5V @200mA | 2x 5V @200mA | ||||||||||
Standby Current | 0.25mA @12V | 0.25mA @ 12V | |||||||||||||||||
Actuator Supplies | 1x 20A | 2x 10A @ Vbatt | |||||||||||||||||
Output Protection | Short to Battery, Ground | ||||||||||||||||||
Battery Input Protection | Overvoltage, Reverse Voltage | ||||||||||||||||||
Survive Voltage | -28V to 36V | ||||||||||||||||||
M110 | M130 | M211 | M220 | M6 Family | M670 | Actuation | M560 | M580 | |||||||||||
Communication | |||||||||||||||||||
High Speed CAN 2.0 | 2x | 4x | 2x | 2x | 2x | 4x | 1x | 4x | 4x | ||||||||||
LIN (master)2 | 2x | ||||||||||||||||||
M110 | M130 | M211 | M220 | M6 Family | M670 | Actuation | M560 | M580 | |||||||||||
Inputs | |||||||||||||||||||
Inputs (Analog or Digital) | 10x | 6x | 9x | 16x | 18x (Digital: 6x; Analog: 12x) | 40x (Digital: 5x switched, 3x Frequency, PWM; Analog: 32) | 4x | 40x (Digital: 9x switched, 3x PWM; Analog: 28) | 44x (Digital: 9x switched, 3x PWM; Analog: 32) | ||||||||||
Reprogramming Enable (FEPS) | 1x @ -18V | 1x @ -18V | 1x @ -18V | 1x @ -18V | 1x @ -18V | 4x | |||||||||||||
Differential VRS | 1x (2 pins) | ||||||||||||||||||
Single Ended VRS | 2x | ||||||||||||||||||
Frequency | 1x | ||||||||||||||||||
Cam Shaft | 2x ±157V | 4x Hall only | |||||||||||||||||
Crank Shaft | 1x ±157V | 1x Hall (VR option) | |||||||||||||||||
RTD Sensor | 7x | 4x | |||||||||||||||||
Knock Sensor | Knock Sensor | ||||||||||||||||||
Lamda Sensor (UEGO) | 2x | ||||||||||||||||||
Lamda Sensor (HEGO) | 4x (only 2x available when using 2x UEGO) | ||||||||||||||||||
Ignition Sense | 1x | 1x | 1x | ||||||||||||||||
M110 | M130 | M211 | M220 | M6 Family | M670 | Actuation | M560 | M580 | |||||||||||
Outputs | |||||||||||||||||||
Low Current Low Side Drives | Up to 1x 20mA & 2x 100mA & 6x 500mA | Up to 6x 500mA LSD | 12x 100mA, 3x 400mA, 14x 700mA, 2x 1A | 11x 100mA, 4x 400mA, 14x 700mA, 2x 1A | |||||||||||||||
Medium Current Low Side Drives | Up to 4x 2A | Up to 4x 2A LSD | |||||||||||||||||
High Current Low Side Drives | 4x 2.2A, 1x 3.2A | 4x 2.2A, 1x 3.2A | |||||||||||||||||
0-5 V Analog Output | Up to 2x 10mA | Up to 2x 10mA | |||||||||||||||||
PWM Low Side | 2x 100mA | 2x 100mA, 2x 250mA & 6x 2A | |||||||||||||||||
H-Bridge | 1x 5A | 2x 8A | 1x 5A full-bridge & 2x 10A full-bridge or 4x 10A half-bridge | 2x 50A peak or 10A | 1x 10A, 2x 5A, 1x 3.2A | 1x 10A, 2x 5A, 1x 3.2A | |||||||||||||
High Side Switch | 1x 15A | 1x Hall (VR option) | |||||||||||||||||
Low Side Injector | 1x 15A or 5A | 3x 5A peak/ 2A hold | 8x software-programmable waveform peak-and-hold: nominal 25A peak, 15A hold | ||||||||||||||||
Current Monitors | 2x | ||||||||||||||||||
Voltage Monitors | 2x | ||||||||||||||||||
High Side Logic Outputs | 2x 1mA | 2x 1mA | |||||||||||||||||
High Side Outputs | 4x 700mA | 4x 700mA | |||||||||||||||||
Low Side General Purpose, PWM (SM, VM, CTM) | 1x 10A, 1x 2A, 1x 500mA | 9x 0.2/0.5A lamp & relay, with monitoring of state, voltage, and fault status | |||||||||||||||||
Low-side General Purpose, Spark (SM) | 1x 8A | 8x (Smart Coil only) with monitoring of state; on-off mode for non-spark uses | |||||||||||||||||
High-side Injector sources | 2x Injector High-Side outputs with programmable boost voltage phase, 25A peak | ||||||||||||||||||
Low side GP (General Purpose) (VM, CTM) | 1x 8A, 2x 6A peak / 4A hold, with voltage and current-tripped monitoring | ||||||||||||||||||
High-side GP (General Purpose) (CM) | 2x 8A up to 85°C, intended for source to low-side outputs, with current monitoring | ||||||||||||||||||
Constant-Current (with inductive actuator) | 8x 2A | ||||||||||||||||||
M110 | M130 | M211 | M220 | M6 Family | M670 | Actuation | M560 | M580 | |||||||||||
Compatibility | |||||||||||||||||||
Vibration | ISO 16750-3 | ISO 16750-3 | 6g random RMS | 6g random RMS | Ford IIIB - Severe | ISO 16750-3 | IEC 60068-2-64 | ISO 16750 chassis mount | ISO 16750 chassis mount | ||||||||||
Environmental Protection | IP67 - Sealed | IP67 – sealed | IP67 | IP69K | IP67 Sealed/Gore vent | IP69K | IP69K & IPx8 Sealed/Gore vent | IP69K Sealed/Gore Vent | IP69K Sealed/Gore Vent | ||||||||||
ESD | ±8kV - SAE J1113-13 | SAE J1113-13 | |||||||||||||||||
Conducted and Radiated Emissions | CISPR25 Class 2 | CISPR25 Class 2 | |||||||||||||||||
Conducted Transients | ISO 7637-2 | ISO 7637-2 | |||||||||||||||||
Bulk Current Injection Immunity | ISO 11452-4 | ISO 11452-4 | |||||||||||||||||
M110 | M130 | M211 | M220 | M6 Family | M670 | Actuation | M560 | M580 | |||||||||||
Physical | |||||||||||||||||||
Material | Plastic (PPA GF33) | PPA GF33 | Aluminum | Aluminum | Aluminum | Aluminum | Aluminum | Aluminum | Aluminum | ||||||||||
Dimension in mm (W x H x D) | 138 x 130 x 42 | 138 x 130 x 42 mm (L x W x H) | 155 x 115 x 46 | 155 x 115 x 39 | 228 x 158 x 50 | 266 x 299 x 56.5 | 207 x 104 x 45 | 225 x 205 x 45 | 225 x 205 x 45 | ||||||||||
Weight | 520g | 520g | 1.02 kg | 2.5 kg | 540g | 1.1 kg | 1.1 kg | ||||||||||||
Connectors | 2 x 20 pin (Molex MX-150) | 2 x 20 pin (Molex MX-150) | 46 pin | 46 pin | 46 pin | Molex CMC 154-pin, 3-pocket | 1x 23 TE (AMSEAL) | Molex 112pin (1x 48, 2x 32) | Molex 112pin (1x 48, 2x 32) | ||||||||||
Location | Chassis mount | Chassis mount | Chassis mount | Engine Compartment/ Chassis | Engine Compartment / Chassis | Passenger Compartment | Chassis/Passenger Compartment | Chassis/Passenger Compartment | |||||||||||
Operating Temperature | ISO 16750-4 (-40°C to 85°C) | -40°C to 85°C | -40°C to 85°C | -40°C to 85°C | -40°C to 85°C | -40°C to 85°C | -40°C to 85°C | -40°C to 85°C | -40°C to 85°C | ||||||||||
M110 | M130 | M211 | M220 | M6 Family | M670 | Actuation | M560 | M580 | |||||||||||
Other | |||||||||||||||||||
Program Status LED drive | 1x | ||||||||||||||||||
Reprogramming Enable In | 1x @18V |